Shoe Moulding
Investment Powder
Gold Star Shoe Cast
Gold Star Shoe Cast is specifically designed for the manufacture of aluminium shoe mould plates for the production of shoe soles. This method of manufacture is used to produce soles for many of the leading names in the training shoe industry.
A typical master shoe model is constructed from wood, metal, or plastic. Silicone is then poured over the master model and left to cure. Once set, the Silicone mould is stripped from the master, Gold Star Shoe Cast slurry is poured into it and allowed to set.
The Gold Star Shoe Cast plaster model is removed from the silicone mould and dried out in the furnace. The plaster model is then set into a frame and molten aluminium is poured over it, the metal is left to cool and the plaster is removed from the aluminium casting. To find out more click the GRS logo

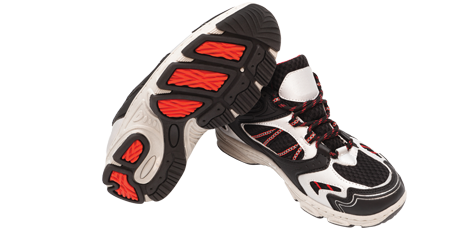

Technical Specification
Mixing Instructions
Shoe Cast is to be mixed at a recommended slurry temperature of 21°C, adjust the water temperature to achieve this.
Add the powder to the water at a ratio of 40:100 and mix for 4 minutes, vacuum the mixing bowl for 1 minute and pour around the pattern. Vacuum for a further 1 minute and then top off the pattern frame. To aid the removal of air bubbles gently vibrate during vacuuming. Total work time is 10 minutes.
The mould must be allowed to set for a minimum of 2 hours before being loaded into a drying oven at ambient temperature. The drying oven is to be ramped up to a temperature of 280alt="image"C at a rate of no greater than 100alt="image"C per hour. The mould must be held at 280alt="image"C for between 5 and 12 hours depending upon its size.
Once the cycle is complete, the drying oven may be switched off and allowed to cool to ambient temperature. The molten metal may then be cast into the mould and allowed to cool, at which point the plaster is removed.
![]() |
Shoe Casting (0.34MB) |
Unable to open PDF documents? Please download Adobe Reader for free from Adobe's website.