BEST PRACTICE
MIXING HINTS AND TIPS
Mixing Hints and Tips
- Ensure correct powder-to-water ratio is used.
- Never add water to powder as it will become lumpy when mixing (always make sure you add water first).
- Aim for a slurry temperature of 21°C for optimum casting results.
- Use clean de-ionised water for investing.
- Weigh out powder and water rather than using any other method of measurement.
- Regularly service and charge oil in your vacuum pump for bubble-free castings.
- Regularly calibrate weigh scale to achieve optimum powder & water weights.
Burnout Hints and Tips
- Do not begin burnout process until 90 minutes after investing.
- If flasks are to be left for more than 4 hours before burning out, place a damp towel over the tops of the flasks to stop them drying out. If this is not done, casting faults may occur.
- Do not exceed 630°C at any stage of the burnout when casting stone in place.
- Decreasing the length of your burnout will increase throughput, but may produce a lower standard of surface finish or, in some cases, lead to mild flashing.
- You will achieve better results fast-firing Vacuum Flasks rather than Centrifugal Flasks, as the perforations in the Vacuum Flasks increase the investment surface area, enabling the release of moisture from the flask during the first stage of the burnout. Centrifugal Flasks may show signs of flashing when very rapidly fired.
- Ensure flask holds at casing temperature for a minimum of 1 hour; it will take this length of time for the core of the flask to fall to the temperature read-out of the furnace.
- Have your furnace calibrated every 6 months as a standard.
- Ensure you have a high-quality digital temperature controller for your furnace (available from www.goldstarpowders.com)
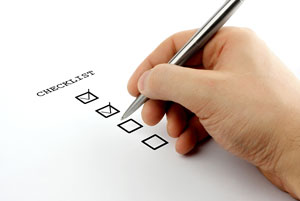

Troubleshooting
Training
Gold Star offers tailor-made training courses to suit your learning needs in Investing & Casting at one of our factory sites, or at your own facility by special arrangement.
Gold Star Training Locations:
UK - Staffordshire India - Chennai China - Panyu Thailand - Bangkok Brasil - Sao Paulo